Daily Maintenance Guide for Precast Concrete Slab Machines: Maximize Lifespan and Production Quality
Daily maintenance of precast concrete slab machines is important. It helps keep them running well, reduces downtime, and ensures high-quality concrete slabs. Whether you’re running a large-scale precast factory or a modular construction plant, regular care not only extends machine life but also improves production efficiency and product consistency.
This article outlines the key areas of maintenance and actionable steps for keeping your precast concrete slab machine in peak working condition.
🧼 1. Daily Equipment Cleaning
🔹 General Cleaning
After every production cycle, remove residual concrete, mortar, or dust from the machine surfaces using soft brushes, water, and cleaning cloths. Pay special attention to the outer housing, conveyors, and feeding systems. Hardened concrete residue can corrode machine parts and interfere with moving components over time.
🔹 Mold Cleaning
Molds are critical for determining the dimensional accuracy and surface quality of precast slabs. After each use, thoroughly clean the molds, especially in corners and hard-to-reach areas. Use dedicated mold release agents and specialized tools to prevent buildup that can affect future slab quality or demolding efficiency.
⚙️ 2. Mechanical Components Maintenance
🔸 Transmission System (Belts, Chains, Gears)
Check belts and chains for proper tension.
- Loose belts may slip and reduce power transmission efficiency.
- Slack chains may cause sudden machine stops or damage.
Adjust tensioners periodically and replace worn components to maintain smooth operation.
🔸 Reducer (Gearbox) Maintenance
The reducer ensures appropriate operating speeds.
- Monitor lubricating oil levels regularly.
- Replace the oil based on operational hours or as per the machine manual.
Insufficient lubrication leads to overheating and accelerated wear.
🔸 Motor Maintenance
- Keep motor surfaces free of dust to prevent heat buildup.
- Regularly check insulation resistance, load current, and bearing condition.
- Lubricate bearings with proper grease at recommended intervals to ensure long-term reliability.
🛢️ 3. Lubrication System Maintenance
🟢 Lubrication Schedule
Apply grease or lubricating oil to shafts, guide rails, and joint components regularly. For instance, high-friction areas like the main spindle may require weekly lubrication.
🟢 System Check
Inspect oil pipelines for blockages or leaks.
- A blocked line can starve components of lubrication.
- Leaks waste oil and may damage nearby electronics or slabs.
Replace or repair damaged pipes promptly.
⚡ 4. Electrical System Maintenance
🔌 Circuit Inspection
Inspect power lines, sensor cables, and control wires for:
- Cracks, frays, or loose connections
- Damaged insulation that could lead to electrical faults or unsafe conditions
Use insulating tape or replace cables as needed to ensure stable current flow.
🔌 Component Function Check
- Test relays, switches, sensors, and contactors for accurate operation.
- Replace any component with ablated contacts or delayed response to avoid system failures.
🧩 5. Mold Maintenance
📐 Accuracy Inspection
Use measuring tools to detect any warping or wear in the molds. Over time, molds may deform and compromise slab precision. Recalibrate or replace molds as needed to maintain slab quality.
🛡️ Anti-Corrosion Treatment
Apply anti-rust oil after cleaning, especially if the molds will be idle. Store molds in a dry, ventilated area to prevent corrosion and extend service life.
🧪 6. Regular Testing and Debugging
🧾 Performance Testing
At least monthly, run full no-load and load tests on the precast concrete slab machine. Check for:
- Unusual noise or vibration
- Synchronized operation of all components
- Output slab quality and dimensional conformity
⚙️ Parameter Calibration
Calibrate vibration frequency, pressure, and slab extrusion speed. Keeping parameters aligned with factory settings ensures stable and repeatable slab production.
✅ Conclusion: Long-Term Value Through Preventive Maintenance
Daily maintenance of your precast concrete slab machine is not just routine—it’s a proactive strategy to protect your investment. With consistent care:
- Equipment operates more reliably
- Slab quality remains consistent
- Operational costs are reduced
- Downtime is minimized
For manufacturers in the precast industry, establishing a daily and monthly maintenance checklist will greatly improve production efficiency and product integrity.
📌 Want High-Performance Precast Concrete Slab Machine?
Explore intelligent slab production solutions, full-line support, and technical consulting at:HENAN KELAI INDUSTRIAL CO.,LTD (KELAI®)
🌐 www.kelaiii.com | WhatsApp: +86 17788171295
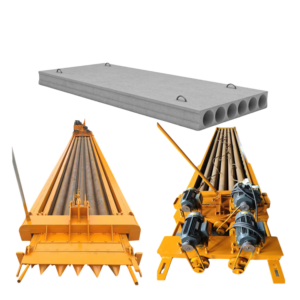